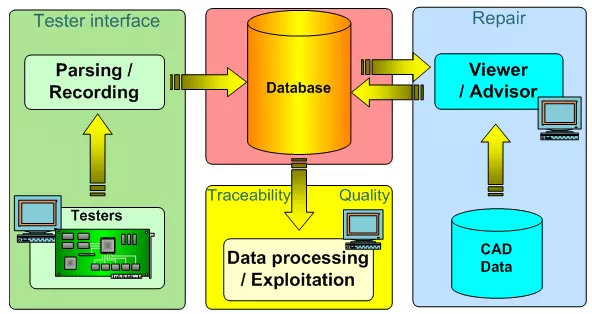
Traceability and Automated repair loop system
QUAD (QUality ADvisor) is a platform agnostic solution that allows seamless implementation into existing MES systems.
The software runs on Windows operated workstations or servers, using a standard SQL interface to manage Oracle, MS-SQL, MaxDB, PostgreSQL etc.
QUAD records everything that happens to a PCBA within your facility, when, by whom and with what. It stores information throughout the assembly steps, allowing full traceability of lots, boards, components and operators.
QUAD offers powerful tools to automate the repair loop system:
- The visual fault diagnostic station allows operators to quickly fix the detected fault and graphically input repair data
- It also provides a history of faults as well as an advisor for repair assistance
- Workflow dashboard to help prioritize shop floor repair operations
Built-in manufacturing analytics such as Statistical Process Control (SPC), allows real-time production monitoring to anticipate the corrective actions, in case of process deviation.
QUAD provides a set of predefined reports that can be selected to configure multiple dashboards for displaying key performance indicators.

K. Coleman
Senior Test Engineer at Megger
They trust us to deliver the best value for their software investment
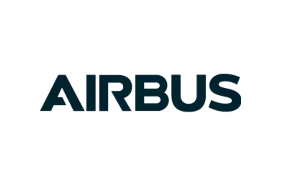
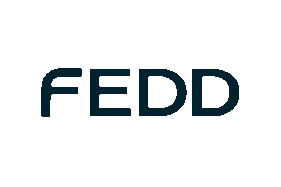
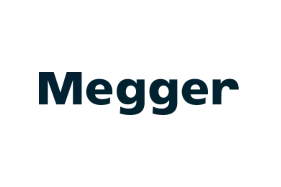
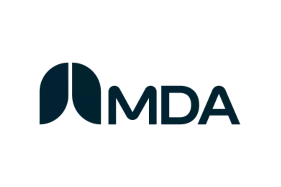
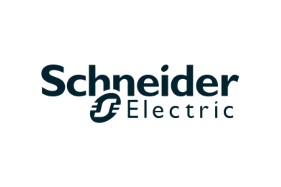
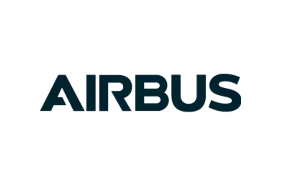
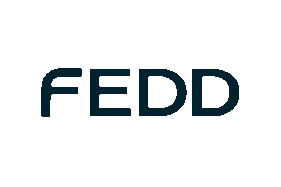
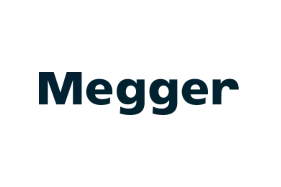
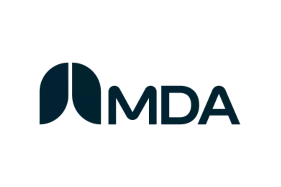
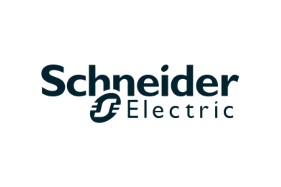
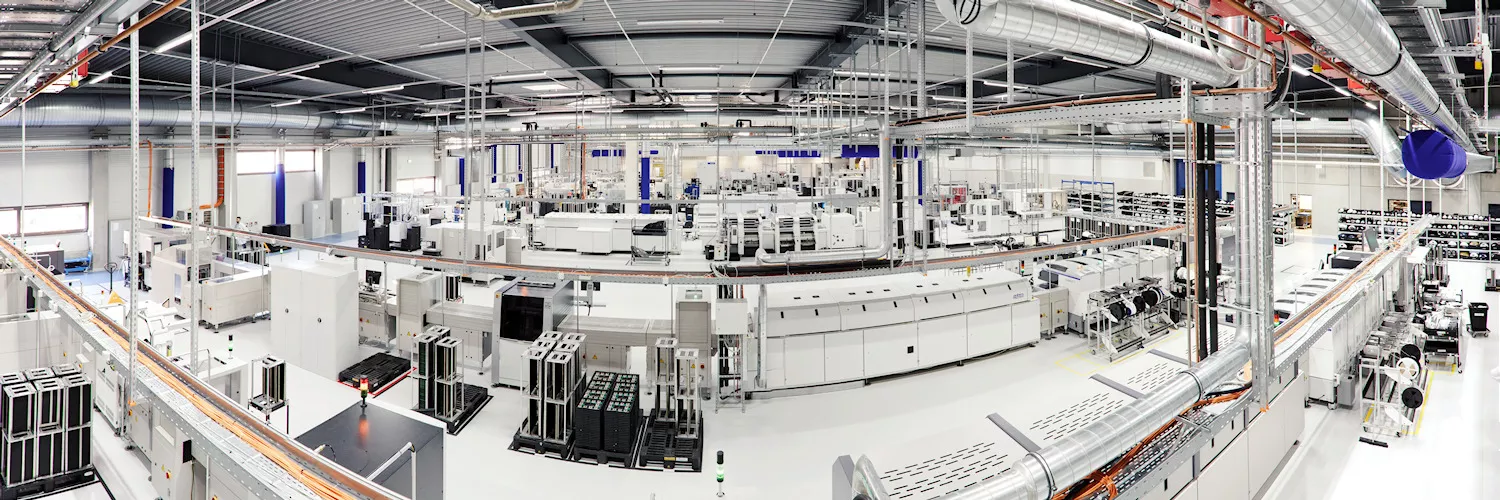
QUAD Software Packages
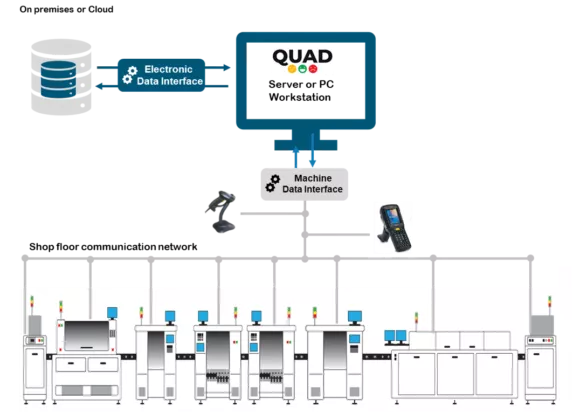
Data logger and traceability
QuadRecorder is the data gathering tool set. It will continually poll specified machines for particular file types (fault tickets) and parse these into the database.
- Interface for assembly, inspection and test machines from any equipment
- QUAD provides a fully documented Open-SQL interface to exchange information with the customer database
- Customer database pulls information from QUAD by sending SQL requests directly or through an Electronic Data Interface (EDI)
The work in progress module, QuadWIP, allows tracking special events like a PCB routing to a specific factory location.
QuadFeederSafe provides full scope of component management, feeder management and process control for full component traceability.
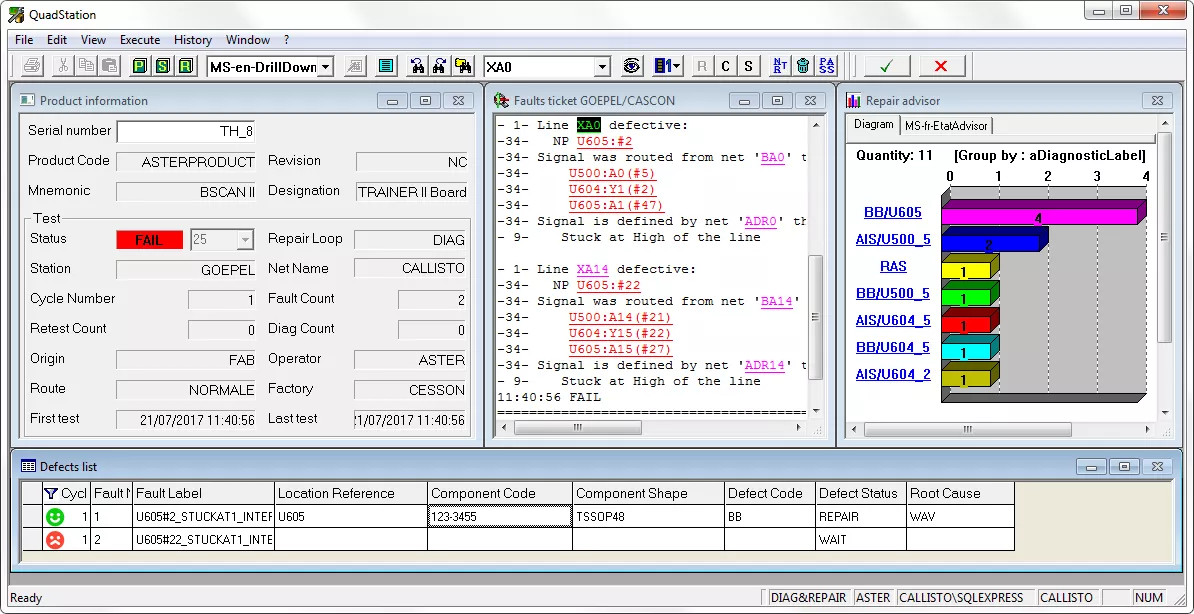
Fault diagnosis station
QuadStation is an interface for fault finding, it displays the PCBA and fault data from the tester, to allow the operator to quickly repair detected faults and to graphically enter the repair data in the database.
During the diagnostic step, the operator has a set of tools to help him in the search for a defect:
- Total interactivity between the schematic, layout, netlist, tester fault ticket, defect data grid and defects advisor bar graph
- Defect advisor facility to allow the operator to have access to statistical fault repartition data
- The web-like navigation in the fault ticket allows users to interactively view the fault location on the schematic and layout viewers
- Repair data is updated in real time for immediate experience sharing

Paperless repair station
The Graphical User Interface (GUI) for both defect entry and paperless repair, uses the viewing features of QuadView for displaying the layout, schematic and netlist views.
- Visualization of the physical layout allows repair technicians to quickly identify components, pins and traces
- Visualization of nails information in layout, schematic and netlist views
- Panel test management with advanced visualization
- Short circuit assistant reduces the time to locate short-circuits
- Fully automated graphical fault code collection
Using the Paperless Repair screen, the user can select the fault to be repaired and allocate the appropriate repair code with one click.
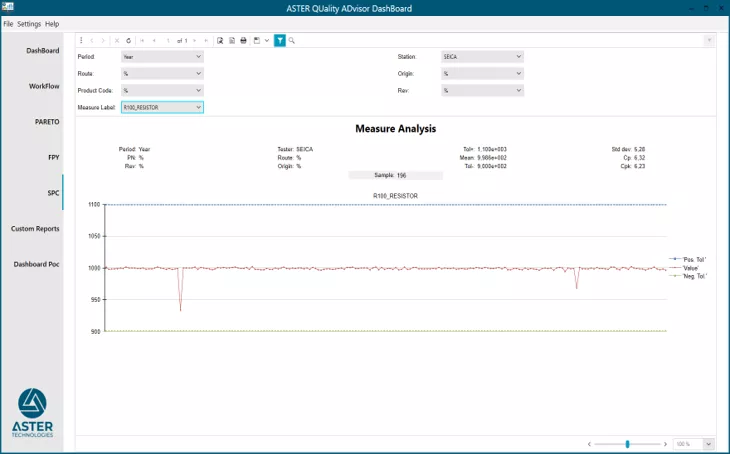
Manufacturing analytics
Built-in manufacturing analytics such as Statistical Process Control (SPC) allows real-time production monitoring to anticipate the corrective actions in case of process deviation.
- Process Capability Analysis (Cp, Cpk) to help make sure that tests constantly achieve the desired level of quality
- First Pass Yield (FPY) from a global level, into more granular statistics for different periods, products, test steps
- Pareto analysis to explore the defect universe from the effective guidance of a top-down approach
Configurable reporting
QuadReports is used to call pre-defined templates and populate these with data from the central database.
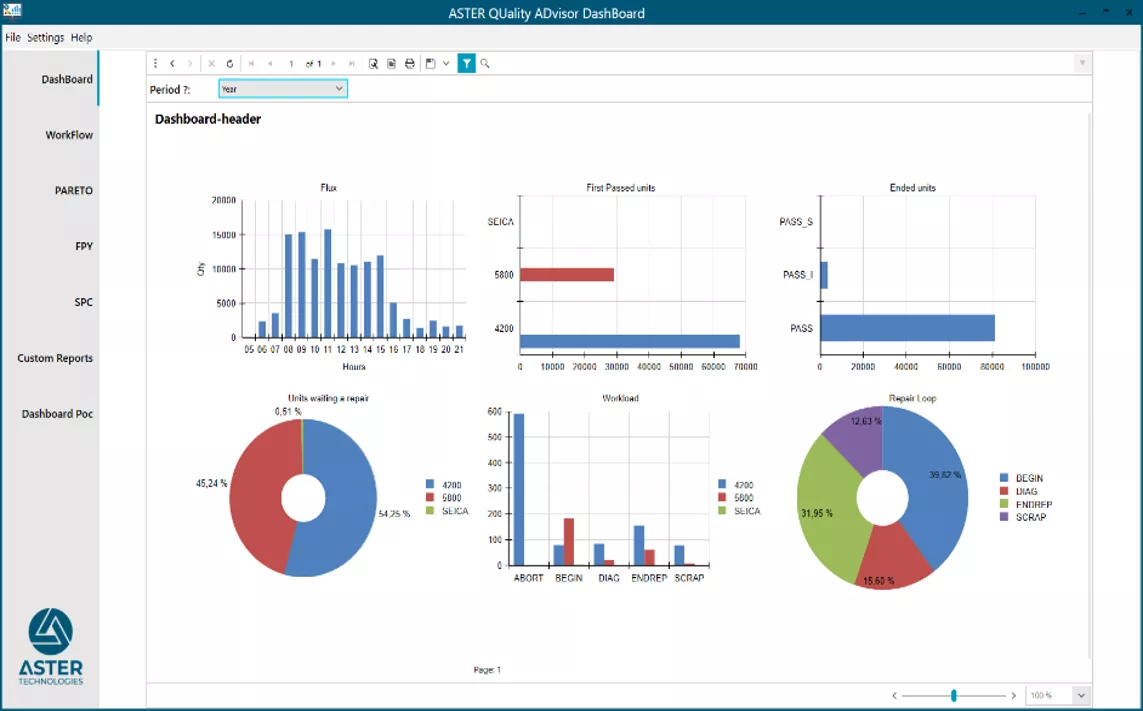
It produces advanced real-time production quality information and reports that can be selected to configure dashboards for displaying key performance indicators.
- Defects and repairs (Yield, Pareto of defects, Workflow…)
- Measures in the test programs (Cp, Cpk, Mean, Repeatability…)
The reports are fully customizable and can be exported in PDF or Excel format.
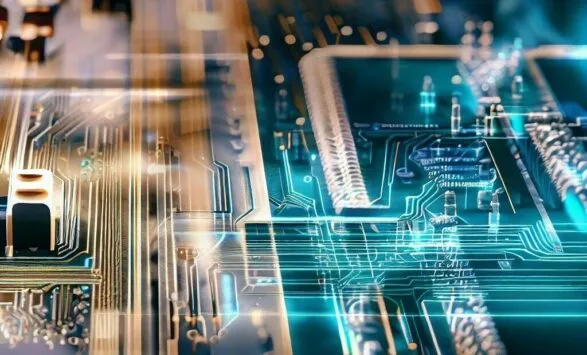
Why ASTER Technologies ?
We offer comprehensive software tools to simulate a PCBA and the manufacturing/test machines in a digital environment. Digital twin technology allows our customers to ensure PCBA fabrication and improve test coverage, to limit the risk of undetected defects, thereby reducing field failures and costly recalls.
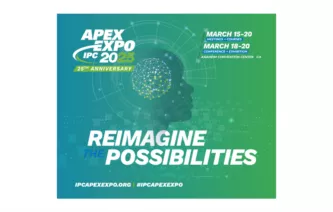